-
Shreya
Hi there! Welcome to my shop. Let me know if you have any questions.
Your message has exceeded the limit.

COMMON-USED MVR: CENTRIFUGAL COMPRESSOR
2022-10-08 18:21:03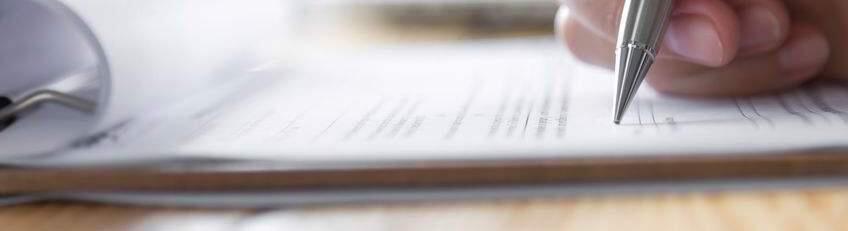
The commonly used vapor compressors mainly include: Roots compressor, axial flow compressor, centrifugal fan and centrifugal compressor. Roots compressor is mainly used for small flow conditions, axial flow compressor is used for large flow conditions, and the axial flow compressor is usually designed as a multi-stage system. And the most common used one is the centrifugal fan and centrifugal compressor.
Centrifugal fan can be used for conditions of low compression ratio, which Π =1.25 maximum. Same with the centrifugal compressor, the gas enters the impeller inlet along the axial, and exits in the radial direction under centrifugal force. The impeller and shell of the fan are welded plate structure, with reinforcing rib reinforcement when necessary. Usually, the gearbox is not required, because the drive system can achieve the required impeller speed.
The main characteristics of a single-stage centrifugal compressor are: the compact arrangement of the overhung impeller and compressor and the gearbox. Motors, gearbox, and compressor are usually mounted on the same base. The compressor housing is of cast or welded construction. Because of a high linear velocity of the impeller which is greater than 400 m/s, the impeller is highly stressed, so it is made of high quality materials such as chromium nickel steel or titanium alloy.
A multistage centrifugal compressor is used for working conditions of high flow rate and high temperature rise of saturation steam. The multistage centrifugal compressor is formed by arranging a number of stages on the same axis. After leaving the first stage, the gas flows through the amplifier and the interstage channel, and then enters the next stage impeller. The impeller shaft runs on the bearing in the housing, driven by separate inclined gears. To improve efficiency and avoid unbearable high temperatures in the housing, water can be injected into the interstage channel. And to achieve a pressure ratio over Π =10, single-stage compressors can also be connected in series. If the impeller is driven by a central drive with several pinion, it may be called a two, three, or four-impeller compressor.